Powrót do listy artykułów
Aktualizowany: 2009-09-11
Efektywność pracy maszyn - wskaźnik OEE - Wskaźnik Wykorzystania Wyposażenia
Coraz większy nacisk kładzie się obecnie na efektywność produkcji i możliwie jak najlepsze wykorzystanie parku maszynowego. Gra idzie często o pojedyncze minuty które pozbierane razem decydują o wyższości nad konkurencją. Jak jednak określić efektywność pracy maszyn? Jak ją policzyć, porównać ? Jak określić czy dana maszyna nie mogła by przypadkiem zrobić więcej i lepiej niż robi dotychczas?
Odpowiedzią jest wskaźnik OEE - Wskaźnik Wykorzystania Wyposażenia (Overall Equipment Effectiveness). Jest on wskaźnikiem określającym efektywność wykorzystania maszyn i urządzeń na podstawie prostej analizy czasów postojów, przezbrajania, awarii i innych czynników wpływających na efektywność.
Czym jest wskaźnik OEE
Ideą powstania wskaźnika OEE była chęć posiadania jedno liczbowego wyznacznika efektywności produkcji. Wyliczamy wskaźnik i patrzymy – wyszło nam dzisiaj 87% a wczoraj było 84% więc od wczoraj coś udało nam się poprawić albo wczoraj coś było nie tak, może awaria, może logistyczny postój.
Upraszczając: Wskaźnik OEE mówi nam że wykorzystaliśmy swoje moce produkcyjne w tylu to a tylu procentach. Upraszczając jeszcze bardziej: nasza maszyna czy linia pracowała X% czasu który pracować powinna. Ale uwaga, X% ZAPLANOWANEGO czasu.
Wskaźnik OEE jest wypadkową trzech innych wskaźników:
• Dostępność - Stosunek czasu zaplanowanego na realizację zadania do czasu który w rzeczywistości możemy na to zadanie poświęcić. Dostępność obniżana jest przez awarie i zależnie od przyjętej metody przez przezbrajanie i ustawianie maszyn.
• Wykorzystanie – Stosunek czasu dostępnego do rzeczywistej pracy. Dostępność jest zaniżana przez straty prędkości wykonywania operacji. Inaczej mówiąc – skoro maszyna miała pewną pulę czasu na pracę to powinna przez te czas wyprodukować pewną ilość produktu – wskaźnik wykorzystania pokazuje nam na ile to się udało.
• Jakość – Stosunek ilości dobrych i wadliwych produktów.
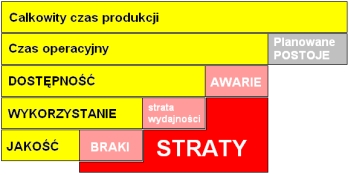
Graficzna prezentacja idei wskaźnika OEE Do tego dodajemy całkowity czas produkcji czyli czas zaplanowany łącznie z wszystkimi planowanymi postojami i rzeczywisty czas produkcji czyli czas na produkcję po odjęciu czasu tychże zaplanowanych planowanych przerw.
OEE = Dostępność x Wykorzystanie x Jakość
Tyle teoria. W praktyce na wartość wskaźnika OEE wpływ ma wiele czynników - przede wszystkim podstawa czasu. Na ogół, według podręczników OEE wylicza się przyjmując za podstawę 8 godzin, czyli typową zmianę roboczą. Ni jak się to ma do rzeczywistości – w praktyce albo produkujemy kilka serii na zmianę albo jedna seria produkowana jest przez kilka zmian.
Czytelnik powie – no dobrze – ale stosując wskaźnik chciałbym ocenić pracę zespołów produkcyjnych a te pracują po 8 godzin. Można i tak ale wiąże się to z pewnym niebezpieczeństwem. Powiedzmy że 1 zmiana przygotowuje produkcję na linii produkcyjnej – musi ją ustawić, zmienić surowiec, przeprogramować sterowniki. A pracownicy drugiej zmiany przejmują pracującą już maszynę. Mamy więc dwa różne wyniki produkcji, z reguły niekorzystne dla tej pierwszej zmiany. Ale czy to oznacza że pracownicy tej zmiany pracowali gorzej ?
Następną ważną sprawą jest interpretacja czasu poświęconego na przezbrajanie/ustawianie maszyn – czy jest on stratą czy nie. Jedni twierdzą że tak – że każda minuta poświęcona na przestawienie maszyny jest stratą. Nie powinno się w ten sposób podchodzić do zagadnienia – przecież nie można produkować innego asortymentu bez zmiany ustawień a ta musi trwać. Idealnym rozwiązaniem jest określenie czasu potrzebnego na przestawienie maszyny – jeśli obsługa zmieści się w tym czasie to nie jest on stratą a jest planowanym postojem. Ze stratą mamy do czynienia wtedy gdy pracownicy wyczerpią pulę czasu przeznaczonego na ustawienie a go nie skończyli.
Błędne jest też często spotykane przeświadczenie że OEE 100% to praca 24 godziny na dobę, 7 dni w tygodniu 31 dni w miesiącu. OEE =100% osiągniemy gdy nasz park maszynowy przepracuje 100% zaplanowanego czasu pracy.
Policzmy więc wskaźnik OEE
Najpierw zdefiniować musimy czas dla którego będziemy wyznaczali wskaźniki. Może to być wspomniane wyżej podręcznikowe osiem godzin ale może to też być np. czas od rozpoczęcia danej serii albo czas jaki miną od początku miesiąca itd. Czas ten będziemy nazywać CZASEM ZAMÓWIONYM bo w rzeczywistości planując produkcję musimy „zamówić” jakiś fizyczny czas na wykonanie danej partii. I wcale nie oznacza to że przez cały ten czas będziemy produkowali – mówimy: produkowaliśmy tę partię od czwartku, od 17 do wtorku, do 12. No ale niedziela była wolna.
Mamy więc czas zamówiony ale jak powiedzieliśmy – nie cały ten czas poświęcony jest na produkcję. Czas zamówiony zwany jest też często całkowitym czasem produkcji. Następnie wyznaczamy CZAS OPERACYJNY zwany też planowanym czasem produkcji. Wyznaczamy go odejmując od czasu zamówionego czas planowanych postojów. Od godziny 17 w czwartek do godziny 12 we wtorek mamy 113 godzin i to jest nasz czas zamówiony. Pracujemy w systemie trzy zmianowym ale w sobotę pracowała tylko 1 zmiana a niedziela była wolna.
Mieliśmy więc 24+16 = 40 godzin planowanego postoju. No i mamy jeszcze przerwy na posiłki – powiedzmy że w sumie była to jedna godzina.
Więc nasz czas operacyjny wynosi 113 – 40 – 1 = 72 godziny.
Następnym składnikiem jest DOSTĘPNOŚĆ czyli czas przez który maszyna była dostępna, czyli mogliśmy na niej cokolwiek wyprodukować.
Dostępność maszyny ograniczają dwa składniki: awarie i przezbrajanie. No i dochodzimy tu do najbardziej kontrowersyjnej części wyliczania wskaźnika OEE. Czy przezbrajanie maszyny czyli przygotowanie jej do produkcji (zmiana narzędzi, form, oprogramowania, ustawień) jest stratą czy nie jest ? Jedni twierdzą że jest stratą bo OEE ma pokazywać proporcje do całkowitego czasu. No ale przecież nie da się zmienić produktu bez zmiany ustawień maszyn – trzeba to zrobić i koniec. Inni z kolei twierdzą że właśnie dla tego że przezbrojenie jest nieuchronne to stratą nie jest.
Jak jest naprawdę? Przeanalizujmy prosty przykład – mamy dwie identyczne linie, każda z nich potrzebuje 10 godzin na zmianę asortymentu. Pierwsza przez miesiąc była przestawiana 7 razy druga 40 razy. A więc pierwsza maszyna z całą pewnością wyprodukowała więcej produktu.
Czy powiemy więc że pierwsza produkowała wydajniej od drugiej ? Przecież druga realizowała plan produkcji tak samo dobrze jak pierwsza.
A ze wyprodukowała mniej produktu z uwagi na częste zmiany? No przecież tak jej pracę zaplanowaliśmy – wielokrotność zmian asortymentu jest stratą ale obciąża dział planowania a nie produkcję.
Dlatego należy przyjąć że przezbrajanie jest stratą ale tylko i wyłącznie ten czas który niepotrzebnie przedłużył ów proces. Innymi słowy określamy czas optymalny dla przezbrojenia – np. 10 godzin i jeśli się w nim zmieścimy to nie jest on stratą.
Odliczamy więc od czasu operacyjnego 10 godzin na przezbrojenie. Uzyskujemy czas operacyjny 72-10 = 62 godziny.
Dla naszego przykładu przyjmijmy że w sumie mieliśmy 3 godziny awarii. I że w rzeczywistości przezbrajanie trwało nie 10 a 12 godzin.
Dostępność naszej maszyny policzymy więc jako czas operacyjny odjąć czas awarii odjąć utracony czas przezbrajania czyli czas dostępny = 62 – 3 –2 = 57 godzin. Dostępność w procentach wynosi (57x100) /62 = 91.9% czasu operacyjnego.
Mamy więc przez 57 godzin dostępną maszynę i zgodnie z naszymi oczekiwaniami przez taki czas powinna efektywnie pracować. Ale rzeczywistość jest daleka od ideału – podczas pracy maszyny mamy do czynienia z wieloma czynnikami zakłócającymi ich pracę: spadki szybkości, chwilowe zatrzymania, uzupełnianie surowca. Istnieje wiele czynników które powodują że maszyna nie wykorzystuje w pełni swoich możliwości. Czyli nie jesteśmy w stanie jej w pełni wykorzystać. No i mamy kolejny składnik współczynnika OEE – WYKORZYSTANIE. Wykorzystanie to czas dostępny pomniejszony o czas strat wynikających ze spadków wydajności. Podręcznikowo stratę tę liczymy w ten sposób że określamy czas na wyprodukowanie 1 sztuki produktu i mnożymy przez ich ilość.
Na potrzeby naszego przykładu przyjmijmy że czas potrzebny na wykonanie 1 produktu wynosi 10 sekund i że przez 57 godzin wyprodukowano 18500 sztuk (łącznie z brakami !). Wedle technologii czas potrzebny na wyprodukowanie 18500 sztuk wynosi 18500 x10s = 43.8 godziny.
Zatem gdzieś nam „uciekło” 13.2 godziny. Wykorzystanie wynosi więc (43.8x100)/57 = 76.8%
Napisałem wyżej że maszyna wykonała 18500 sztuk wyrobu wraz z brakami. Zamówienie natomiast opiewało na 18000szt. Czyli wyprodukowano 500 wadliwych sztuk. Czyli maszyna musiała poświecić czas na „do produkowanie” tych brakujących sztuk. Aby więc obraz sytuacji był jasny wprowadzamy następny składnik: JAKOŚĆ. Jakość to stosunek wyrobów dobrych do wadliwych czyli w naszym przykładzie
(18000x100)/18500 = 97.2%
Mamy więc wyliczone procentowe wartości składników więc wyliczmy OEE:
Współczynnik OEE = Dostępność x Wykorzystanie x Jakość czyli dla powyższych danych:
OEE = 91.9% x 76.8% x 97.2% = ((91.9/100) x (76.8/100) x (91.9/100))*100 = 68.6%
Podsumujmy nasz przykład
• Czas zamówiony: 113 godzin - tyle czasu minęło od rozpoczęcia do zakończenia badanego procesu produkcyjnego
• Czas operacyjny: 62 godziny – czas pomniejszony o planowane postoje które nie są stratą i pomniejszony o zaplanowany czas przezbrojenia maszyny który też stratą nie jest.
• Dostępność: 91.9% (57 godzin) – od czasu operacyjnego odejmujemy czas awarii który jest stratą oraz czas o który przekroczono czas przezbrojenia który też jest stratą.
• Wykorzystanie: 76.8% - utracono 13.2 godziny z czasu dostępności maszyny na skutek spowolnienia jej pracy albo co ważne na skutek błędnego założenia czasu potrzebnego na realizację zlecenia np. przyjęcie w planowaniu katalogowej a nie rzeczywistej wydajności maszyny.
• Jakość: 97.2% - wyprodukowano 500 wadliwych sztuk produktu. Pomijamy w naszym przykładzie od straty surowca – nie tym się tutaj zajmujemy. Ale skoro zabrakło nam 500 sztuk to musimy je dodatkowo wyprodukować na co trzeba poświęcić dodatkowe 1.36 godziny.
• OEE: 68.6% - oznacza że nasza maszyna przepracowała efektywnie 68.6% czasu który mogła by przepracować gdyby wszystko odbywało się zgodnie z planem produkcyjnym, nie było awarii, przezbrajanie wykonane było w planowanym czasie a maszyna pracowała idealnie bez żadnych strat wydajności i nie wyprodukowała by tylu braków.
Praktyczna wartość współczynnika OEE
Wartość współczynnika OEE jest ściśle zależna od pracy maszyn ale jego wartość nominalna zależy od metod obliczeniowych i procedur pozyskiwania danych. Powiedzenie że zakład A ma lepszą wydajność bo ma lepszy o 5% wskaźnik OEE niż zakład B jest prawdziwe tylko i wyłącznie jeśli specyfika produkcji i metody obliczeniowe są identyczne – a to się w praktyce nie zdarza.
Dlatego należy traktować OEE jako wskaźnik wewnętrzny – jako jedno liczbowy wskaźnik pozwalający oszacować poprawę lub pogorszenie sytuacji w porównaniu do sytuacji z innego okresu na tej samej linii produkcyjnej, maszynie lub grupie maszyn.
Tak jak w praktyce sam wskaźnik OEE jest tworem trochę „księżycowym” i tak naprawdę niewiele nam mówi o przyczynach utraty efektywności tak jego składniki poddane gruntownej analizie pozwalają często uzyskać bardzo znaczącą poprawę, szczególnie przez skracanie czasu przestawiania maszyn – bo właśnie przestawianie maszyn i zmiana asortymentu jest miejscem gdzie można znaleźć wiele cennych godzin.
Metody pomiaru
Metod pomiaru jest wiele. Najprostsza i najbardziej popularna a jednocześnie najmniej efektywna metoda to wypełnianie arkuszy strat gdzie zakłada się jako czas zamówiony 8 godzin a pracownicy wpisują poszczególne wartości postojów, przestojów itd. Potem ktoś to zlicza, wpisuje do jakiegoś arkusza, robi wykresy etc. Niestety metoda taka jest obarczona trzema podstawowymi wadami: po pierwszej już wspomniałem – 8 godzin podstawy czasu ni jak się nie ma do rzeczywistości. Druga wada to rzetelność takiej metody, jak to się mówi: papier jest cierpliwy.
Trzecia wada to fakt że niezmiernie rzadko zestawiania z tak prowadzonych zapisów robione są na bieżąco. Najczęściej jest to raport robiony raz na miesiąc. Problem polega na tym że informacja o takiej to a takiej efektywności w skali miesiąca jest mało użyteczna. Jeżeli z obserwacji pracy maszyny wyszło nam że utracono dwie godziny teraz, czyli dzisiaj, ewentualnie wczoraj wieczorem to jesteśmy w stanie dojść do przyczyn tej straty – choćby przez wywiad z operatorem czy ogląd zapisów z telewizji przemysłowej. Jednak informacja że w ubiegłym miesiącu straciliśmy 48 godzin nie ma większej praktycznej wartości bo pokazuje co prawda że jest źle, ale nie pokazuje dla czego! Aby poprawić efektywność trzeba to robić ciągle, ustawicznie, godzinę po godzinie, dzień po dniu lokalizować źródła strat i je usuwać. Raport stworzony raz na miesiąc można tak na prawdę powiesić na korkowej tablicy żeby tam sobie ładnie wyglądał.
Dostępne też są programy do zbierania informacji gdzie dane wpisywane są do stosownych formularzy a program przetwarza je na bieżąco.
Jest to rozwiązanie dużo wygodniejsze ale nadal obarczone niebezpieczeństwem wpisywania cokolwiek „niedokładnych” danych.
Idealnie więc byłoby mieć takie „coś” co będzie samo obserwowało pracę maszyn i będzie „wiedziało” co się dzieje aby samodzielnie wyliczyć OEE i jego składniki. Takie „coś” istnieje – to systemy MES (Manufacturing Execution System) czyli w wolnym tłumaczeniu systemy kontroli wykonania produkcji. Systemy takie importują dane z systemów SCADA (systemy do wizualizacji pracy maszyn i instalacji przemysłowych) dzięki czemu wiedzą jak pracuje dana linia oraz dane z systemów ERP (Planowanie produkcji) dzięki czemu wiedzą co robione być powinno.
System MES powinien być marzeniem każdego szefa produkcji ale niestety dla większości marzeniem pozostanie – oprogramowanie MES to konieczność integracji wielu systemów IT i automatyki co wiąże się z bardzo dużymi kosztami, wymaga bardzo dużo czasu i znacznego zaangażowania ze strony inwestora. Często wdrożenie takiego systemu nie jest możliwe w akceptowalnym zakresie kosztów.
Dostępne są też systemy dedykowane o znacznie mniejszym stopniu integracji z systemami biznesowymi przedsiębiorstwa ale za to znacznie tańsze i zdecydowanie przyjaźniejsze we wdrożeniu. Przykładem takiego systemu jest Golem OEE który za pomocą specjalnego interfejsu śledzi sygnały z maszyn (poprzez analogię do zwykłych liczników i liczników czasu pracy) a następnie poddaje je zaawansowanej analizie tworząc szereg raportów o ich pracy z wyliczaniem wskaźników efektywności w czasie rzeczywistym włącznie.
Odpowiedzią jest wskaźnik OEE - Wskaźnik Wykorzystania Wyposażenia (Overall Equipment Effectiveness). Jest on wskaźnikiem określającym efektywność wykorzystania maszyn i urządzeń na podstawie prostej analizy czasów postojów, przezbrajania, awarii i innych czynników wpływających na efektywność.
Czym jest wskaźnik OEE
Ideą powstania wskaźnika OEE była chęć posiadania jedno liczbowego wyznacznika efektywności produkcji. Wyliczamy wskaźnik i patrzymy – wyszło nam dzisiaj 87% a wczoraj było 84% więc od wczoraj coś udało nam się poprawić albo wczoraj coś było nie tak, może awaria, może logistyczny postój.
Upraszczając: Wskaźnik OEE mówi nam że wykorzystaliśmy swoje moce produkcyjne w tylu to a tylu procentach. Upraszczając jeszcze bardziej: nasza maszyna czy linia pracowała X% czasu który pracować powinna. Ale uwaga, X% ZAPLANOWANEGO czasu.
Wskaźnik OEE jest wypadkową trzech innych wskaźników:
• Dostępność - Stosunek czasu zaplanowanego na realizację zadania do czasu który w rzeczywistości możemy na to zadanie poświęcić. Dostępność obniżana jest przez awarie i zależnie od przyjętej metody przez przezbrajanie i ustawianie maszyn.
• Wykorzystanie – Stosunek czasu dostępnego do rzeczywistej pracy. Dostępność jest zaniżana przez straty prędkości wykonywania operacji. Inaczej mówiąc – skoro maszyna miała pewną pulę czasu na pracę to powinna przez te czas wyprodukować pewną ilość produktu – wskaźnik wykorzystania pokazuje nam na ile to się udało.
• Jakość – Stosunek ilości dobrych i wadliwych produktów.
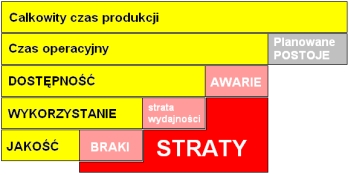
Graficzna prezentacja idei wskaźnika OEE
OEE = Dostępność x Wykorzystanie x Jakość
Tyle teoria. W praktyce na wartość wskaźnika OEE wpływ ma wiele czynników - przede wszystkim podstawa czasu. Na ogół, według podręczników OEE wylicza się przyjmując za podstawę 8 godzin, czyli typową zmianę roboczą. Ni jak się to ma do rzeczywistości – w praktyce albo produkujemy kilka serii na zmianę albo jedna seria produkowana jest przez kilka zmian.
Czytelnik powie – no dobrze – ale stosując wskaźnik chciałbym ocenić pracę zespołów produkcyjnych a te pracują po 8 godzin. Można i tak ale wiąże się to z pewnym niebezpieczeństwem. Powiedzmy że 1 zmiana przygotowuje produkcję na linii produkcyjnej – musi ją ustawić, zmienić surowiec, przeprogramować sterowniki. A pracownicy drugiej zmiany przejmują pracującą już maszynę. Mamy więc dwa różne wyniki produkcji, z reguły niekorzystne dla tej pierwszej zmiany. Ale czy to oznacza że pracownicy tej zmiany pracowali gorzej ?
Następną ważną sprawą jest interpretacja czasu poświęconego na przezbrajanie/ustawianie maszyn – czy jest on stratą czy nie. Jedni twierdzą że tak – że każda minuta poświęcona na przestawienie maszyny jest stratą. Nie powinno się w ten sposób podchodzić do zagadnienia – przecież nie można produkować innego asortymentu bez zmiany ustawień a ta musi trwać. Idealnym rozwiązaniem jest określenie czasu potrzebnego na przestawienie maszyny – jeśli obsługa zmieści się w tym czasie to nie jest on stratą a jest planowanym postojem. Ze stratą mamy do czynienia wtedy gdy pracownicy wyczerpią pulę czasu przeznaczonego na ustawienie a go nie skończyli.
Błędne jest też często spotykane przeświadczenie że OEE 100% to praca 24 godziny na dobę, 7 dni w tygodniu 31 dni w miesiącu. OEE =100% osiągniemy gdy nasz park maszynowy przepracuje 100% zaplanowanego czasu pracy.
Policzmy więc wskaźnik OEE
Najpierw zdefiniować musimy czas dla którego będziemy wyznaczali wskaźniki. Może to być wspomniane wyżej podręcznikowe osiem godzin ale może to też być np. czas od rozpoczęcia danej serii albo czas jaki miną od początku miesiąca itd. Czas ten będziemy nazywać CZASEM ZAMÓWIONYM bo w rzeczywistości planując produkcję musimy „zamówić” jakiś fizyczny czas na wykonanie danej partii. I wcale nie oznacza to że przez cały ten czas będziemy produkowali – mówimy: produkowaliśmy tę partię od czwartku, od 17 do wtorku, do 12. No ale niedziela była wolna.
Mamy więc czas zamówiony ale jak powiedzieliśmy – nie cały ten czas poświęcony jest na produkcję. Czas zamówiony zwany jest też często całkowitym czasem produkcji. Następnie wyznaczamy CZAS OPERACYJNY zwany też planowanym czasem produkcji. Wyznaczamy go odejmując od czasu zamówionego czas planowanych postojów. Od godziny 17 w czwartek do godziny 12 we wtorek mamy 113 godzin i to jest nasz czas zamówiony. Pracujemy w systemie trzy zmianowym ale w sobotę pracowała tylko 1 zmiana a niedziela była wolna.
Mieliśmy więc 24+16 = 40 godzin planowanego postoju. No i mamy jeszcze przerwy na posiłki – powiedzmy że w sumie była to jedna godzina.
Więc nasz czas operacyjny wynosi 113 – 40 – 1 = 72 godziny.
Następnym składnikiem jest DOSTĘPNOŚĆ czyli czas przez który maszyna była dostępna, czyli mogliśmy na niej cokolwiek wyprodukować.
Dostępność maszyny ograniczają dwa składniki: awarie i przezbrajanie. No i dochodzimy tu do najbardziej kontrowersyjnej części wyliczania wskaźnika OEE. Czy przezbrajanie maszyny czyli przygotowanie jej do produkcji (zmiana narzędzi, form, oprogramowania, ustawień) jest stratą czy nie jest ? Jedni twierdzą że jest stratą bo OEE ma pokazywać proporcje do całkowitego czasu. No ale przecież nie da się zmienić produktu bez zmiany ustawień maszyn – trzeba to zrobić i koniec. Inni z kolei twierdzą że właśnie dla tego że przezbrojenie jest nieuchronne to stratą nie jest.
Jak jest naprawdę? Przeanalizujmy prosty przykład – mamy dwie identyczne linie, każda z nich potrzebuje 10 godzin na zmianę asortymentu. Pierwsza przez miesiąc była przestawiana 7 razy druga 40 razy. A więc pierwsza maszyna z całą pewnością wyprodukowała więcej produktu.
Czy powiemy więc że pierwsza produkowała wydajniej od drugiej ? Przecież druga realizowała plan produkcji tak samo dobrze jak pierwsza.
A ze wyprodukowała mniej produktu z uwagi na częste zmiany? No przecież tak jej pracę zaplanowaliśmy – wielokrotność zmian asortymentu jest stratą ale obciąża dział planowania a nie produkcję.
Dlatego należy przyjąć że przezbrajanie jest stratą ale tylko i wyłącznie ten czas który niepotrzebnie przedłużył ów proces. Innymi słowy określamy czas optymalny dla przezbrojenia – np. 10 godzin i jeśli się w nim zmieścimy to nie jest on stratą.
Odliczamy więc od czasu operacyjnego 10 godzin na przezbrojenie. Uzyskujemy czas operacyjny 72-10 = 62 godziny.
Dla naszego przykładu przyjmijmy że w sumie mieliśmy 3 godziny awarii. I że w rzeczywistości przezbrajanie trwało nie 10 a 12 godzin.
Dostępność naszej maszyny policzymy więc jako czas operacyjny odjąć czas awarii odjąć utracony czas przezbrajania czyli czas dostępny = 62 – 3 –2 = 57 godzin. Dostępność w procentach wynosi (57x100) /62 = 91.9% czasu operacyjnego.
Mamy więc przez 57 godzin dostępną maszynę i zgodnie z naszymi oczekiwaniami przez taki czas powinna efektywnie pracować. Ale rzeczywistość jest daleka od ideału – podczas pracy maszyny mamy do czynienia z wieloma czynnikami zakłócającymi ich pracę: spadki szybkości, chwilowe zatrzymania, uzupełnianie surowca. Istnieje wiele czynników które powodują że maszyna nie wykorzystuje w pełni swoich możliwości. Czyli nie jesteśmy w stanie jej w pełni wykorzystać. No i mamy kolejny składnik współczynnika OEE – WYKORZYSTANIE. Wykorzystanie to czas dostępny pomniejszony o czas strat wynikających ze spadków wydajności. Podręcznikowo stratę tę liczymy w ten sposób że określamy czas na wyprodukowanie 1 sztuki produktu i mnożymy przez ich ilość.
Na potrzeby naszego przykładu przyjmijmy że czas potrzebny na wykonanie 1 produktu wynosi 10 sekund i że przez 57 godzin wyprodukowano 18500 sztuk (łącznie z brakami !). Wedle technologii czas potrzebny na wyprodukowanie 18500 sztuk wynosi 18500 x10s = 43.8 godziny.
Zatem gdzieś nam „uciekło” 13.2 godziny. Wykorzystanie wynosi więc (43.8x100)/57 = 76.8%
Napisałem wyżej że maszyna wykonała 18500 sztuk wyrobu wraz z brakami. Zamówienie natomiast opiewało na 18000szt. Czyli wyprodukowano 500 wadliwych sztuk. Czyli maszyna musiała poświecić czas na „do produkowanie” tych brakujących sztuk. Aby więc obraz sytuacji był jasny wprowadzamy następny składnik: JAKOŚĆ. Jakość to stosunek wyrobów dobrych do wadliwych czyli w naszym przykładzie
(18000x100)/18500 = 97.2%
Mamy więc wyliczone procentowe wartości składników więc wyliczmy OEE:
Współczynnik OEE = Dostępność x Wykorzystanie x Jakość czyli dla powyższych danych:
OEE = 91.9% x 76.8% x 97.2% = ((91.9/100) x (76.8/100) x (91.9/100))*100 = 68.6%
Podsumujmy nasz przykład
• Czas zamówiony: 113 godzin - tyle czasu minęło od rozpoczęcia do zakończenia badanego procesu produkcyjnego
• Czas operacyjny: 62 godziny – czas pomniejszony o planowane postoje które nie są stratą i pomniejszony o zaplanowany czas przezbrojenia maszyny który też stratą nie jest.
• Dostępność: 91.9% (57 godzin) – od czasu operacyjnego odejmujemy czas awarii który jest stratą oraz czas o który przekroczono czas przezbrojenia który też jest stratą.
• Wykorzystanie: 76.8% - utracono 13.2 godziny z czasu dostępności maszyny na skutek spowolnienia jej pracy albo co ważne na skutek błędnego założenia czasu potrzebnego na realizację zlecenia np. przyjęcie w planowaniu katalogowej a nie rzeczywistej wydajności maszyny.
• Jakość: 97.2% - wyprodukowano 500 wadliwych sztuk produktu. Pomijamy w naszym przykładzie od straty surowca – nie tym się tutaj zajmujemy. Ale skoro zabrakło nam 500 sztuk to musimy je dodatkowo wyprodukować na co trzeba poświęcić dodatkowe 1.36 godziny.
• OEE: 68.6% - oznacza że nasza maszyna przepracowała efektywnie 68.6% czasu który mogła by przepracować gdyby wszystko odbywało się zgodnie z planem produkcyjnym, nie było awarii, przezbrajanie wykonane było w planowanym czasie a maszyna pracowała idealnie bez żadnych strat wydajności i nie wyprodukowała by tylu braków.
Praktyczna wartość współczynnika OEE
Wartość współczynnika OEE jest ściśle zależna od pracy maszyn ale jego wartość nominalna zależy od metod obliczeniowych i procedur pozyskiwania danych. Powiedzenie że zakład A ma lepszą wydajność bo ma lepszy o 5% wskaźnik OEE niż zakład B jest prawdziwe tylko i wyłącznie jeśli specyfika produkcji i metody obliczeniowe są identyczne – a to się w praktyce nie zdarza.
Dlatego należy traktować OEE jako wskaźnik wewnętrzny – jako jedno liczbowy wskaźnik pozwalający oszacować poprawę lub pogorszenie sytuacji w porównaniu do sytuacji z innego okresu na tej samej linii produkcyjnej, maszynie lub grupie maszyn.
Tak jak w praktyce sam wskaźnik OEE jest tworem trochę „księżycowym” i tak naprawdę niewiele nam mówi o przyczynach utraty efektywności tak jego składniki poddane gruntownej analizie pozwalają często uzyskać bardzo znaczącą poprawę, szczególnie przez skracanie czasu przestawiania maszyn – bo właśnie przestawianie maszyn i zmiana asortymentu jest miejscem gdzie można znaleźć wiele cennych godzin.
Metody pomiaru
Metod pomiaru jest wiele. Najprostsza i najbardziej popularna a jednocześnie najmniej efektywna metoda to wypełnianie arkuszy strat gdzie zakłada się jako czas zamówiony 8 godzin a pracownicy wpisują poszczególne wartości postojów, przestojów itd. Potem ktoś to zlicza, wpisuje do jakiegoś arkusza, robi wykresy etc. Niestety metoda taka jest obarczona trzema podstawowymi wadami: po pierwszej już wspomniałem – 8 godzin podstawy czasu ni jak się nie ma do rzeczywistości. Druga wada to rzetelność takiej metody, jak to się mówi: papier jest cierpliwy.
Trzecia wada to fakt że niezmiernie rzadko zestawiania z tak prowadzonych zapisów robione są na bieżąco. Najczęściej jest to raport robiony raz na miesiąc. Problem polega na tym że informacja o takiej to a takiej efektywności w skali miesiąca jest mało użyteczna. Jeżeli z obserwacji pracy maszyny wyszło nam że utracono dwie godziny teraz, czyli dzisiaj, ewentualnie wczoraj wieczorem to jesteśmy w stanie dojść do przyczyn tej straty – choćby przez wywiad z operatorem czy ogląd zapisów z telewizji przemysłowej. Jednak informacja że w ubiegłym miesiącu straciliśmy 48 godzin nie ma większej praktycznej wartości bo pokazuje co prawda że jest źle, ale nie pokazuje dla czego! Aby poprawić efektywność trzeba to robić ciągle, ustawicznie, godzinę po godzinie, dzień po dniu lokalizować źródła strat i je usuwać. Raport stworzony raz na miesiąc można tak na prawdę powiesić na korkowej tablicy żeby tam sobie ładnie wyglądał.
Dostępne też są programy do zbierania informacji gdzie dane wpisywane są do stosownych formularzy a program przetwarza je na bieżąco.
Jest to rozwiązanie dużo wygodniejsze ale nadal obarczone niebezpieczeństwem wpisywania cokolwiek „niedokładnych” danych.
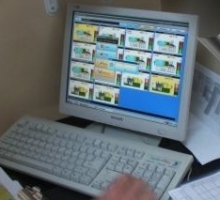
System MES powinien być marzeniem każdego szefa produkcji ale niestety dla większości marzeniem pozostanie – oprogramowanie MES to konieczność integracji wielu systemów IT i automatyki co wiąże się z bardzo dużymi kosztami, wymaga bardzo dużo czasu i znacznego zaangażowania ze strony inwestora. Często wdrożenie takiego systemu nie jest możliwe w akceptowalnym zakresie kosztów.
Dostępne są też systemy dedykowane o znacznie mniejszym stopniu integracji z systemami biznesowymi przedsiębiorstwa ale za to znacznie tańsze i zdecydowanie przyjaźniejsze we wdrożeniu. Przykładem takiego systemu jest Golem OEE który za pomocą specjalnego interfejsu śledzi sygnały z maszyn (poprzez analogię do zwykłych liczników i liczników czasu pracy) a następnie poddaje je zaawansowanej analizie tworząc szereg raportów o ich pracy z wyliczaniem wskaźników efektywności w czasie rzeczywistym włącznie.
- Autor:
- Wojciech Mazurek
- Źródło:
- Neuron
- Dodał:
- Neuron-Wojciech Mazurek
Czytaj także
-
Kluczowa rola wycinarek laserowych w obróbce metali
Wycinarki laserowe zrewolucjonizowały przemysł obróbki metali, oferując niezwykłą precyzję i efektywność. Dowiedz się, dlaczego są one...
-
Jak skutecznie zarządzać komponentami SMD w nowoczesnej produkcji?
Zarządzanie komponentami SMD to proces, który zwykle nie przyciąga uwagi – dopóki wszystko działa sprawnie. Jednak wystarczy jedno...
-
-
-